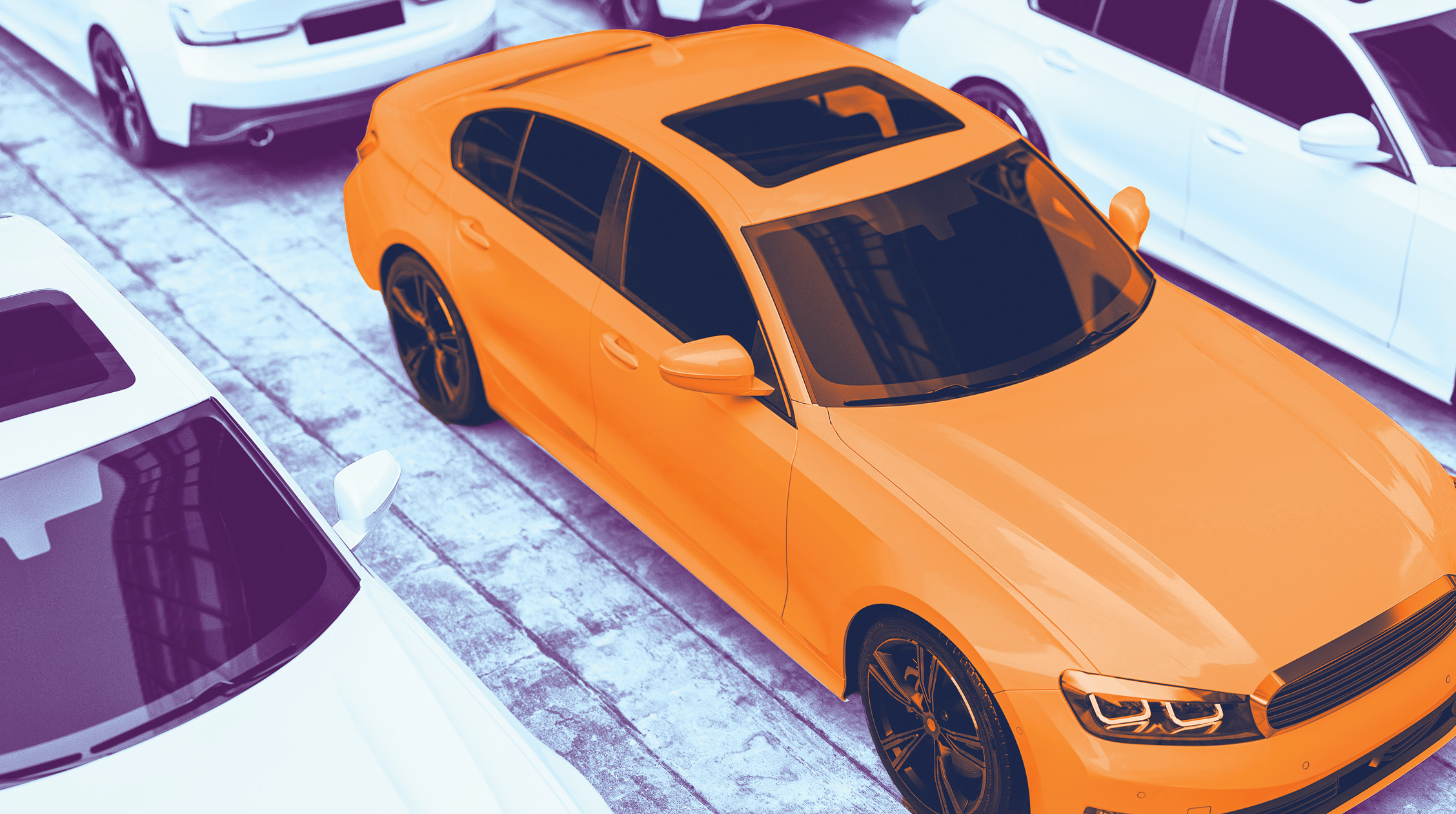
Integrating Digital Twins in Manufacturing
Manufacturers are always looking for ways to innovate, especially in response to new demands. For example, consumers are demanding more complex products whilst also wanting them to be more sustainable. Implementing digital twins in manufacturing is one way that manufacturers are addressing these growing demands and the challenges they present.
A digital twin (DT) is a virtual replica of a physical object, person, or process that can be used to increase understanding and perform tests. DTs are linked to real data sources in the environment and update in real time to reflect changes in the physical world.
Here, we’ll outline the specific ways that DT technology is being implemented in manufacturing and why it is valuable, highlighting leading research on the topic.
Why use digital twin technology?
Digital twins are useful for obtaining information to improve a physical asset. Because of the use of sensors, a large amount of data is collected, which can help inform data-driven decision making. This is particularly valuable for monitoring complex systems, product simulation, and managing an object or process across an entire lifecycle.
DTs have three key characteristics:
- They are an exact representation of a physical system.
- They can be connected along an entire life cycle from design to disposal and/or across entire processes.
- There is an exchange of data back and forth between the physical and digital versions of the asset using sensors.
It’s worth noting that simulations typically study one process, whilst DTs can run any number of simulations to study multiple processes. Moreover, simulations lack the real-time data that characterise a DT.
If you want to learn more about what DTs are and how they work in more detail, see our article What is Digital Twin Technology?
Integrating digital twins in manufacturing
Integrating digital twins into manufacturing processes can be difficult.
Firstly, they require integration into an existing manufacturing environment and a robust IT infrastructure. This may require updating technological capabilities and disrupting the flow of ongoing processes. Secondly, because of the diverse factors that influence a batch of products, it can be hard to map out the variability of production.
So, how do manufacturers begin implementing DT technology?
Ideally, larger DTs are designed by starting with smaller DTs and gradually built up by connecting them together. Individual products or parts of a process can be digitised and then linked together once established. This helps build up technological infrastructure gradually.
Moreover, the design of DTs should be directly linked to the objectives of the business. This helps address the issue of variability and the potentially endless amount of data to collect. DTs can be designed with the aim of reducing costs, making materials more sustainable, or fixing a key snag issue on an assembly line. Designing DTs with your objectives in mind can help direct you towards which data you should collect.
Establishing DTs can create a single and clear source of data that can be accessed across the manufacturing process, enabling cross-discipline collaboration and eventually faster decision making.
Virtual testing
An article in Machines explores the idea of employing a longer vision of a product’s life cycle by using digital twins.
Product quality is highly important for consumers. Manufacturers monitor product quality during the manufacturing process, but they must also ensure its quality is retained throughout its use by the consumer. However, this is difficult and expensive.
The authors reflect that physical testing is not always successful. Not only does it require lots of physical resources, time, and money, but there is a limit to the possible environmental effects that can be tested in physical settings (due to budget and time constraints) compared to what will occur during a customer’s experience using the product.
Therefore, to overcome the constraints of time and space during testing, the authors suggest that DTs can enable the testing of an unlimited number of virtual spaces where manufacturers can take the exact same initial conditions and vary the environmental factors to observe different outcomes. Whilst doing so, there is no need to travel or create physical environments.
Furthermore, time can be controlled too. The simulations can run at any speed, progressing years and decades into the future or even moving by microseconds to observe changes slowly and carefully.
Virtual testing using DTs can support decision making and improve manufacturing processes. But how can they improve manufacturing processes directly?
Implementing digital twins in a factory
An article in Machines explores the process of implementing digitals twins in manufacturing, specifically in a factory environment.
The authors begin by suggesting you should build a virtual representation of the factory. Then, you can validate it using static data to represent the history of the factory’s operations. This enables you to replay history and provide insights into how to optimise the present performance of the factory.
The next step requires real-time synchronisation between the factory and its virtual copy. This involves using sensors and any other necessary forms of data to ensure that the most recent data is automatically applied.
Closed feedback loops
Establishing a factory DT, the authors explain, enables enhanced monitoring and tracking of the factory’s performance. By simulating different scenarios, users can boost their understanding of what could happen in the future, helping them better identify the best course of action.
This is essentially a closed feedback loop, which refers to an automatic control system in which an operation, process, or mechanism is regulated by feedback. For example, it’s like if a company conducts customer surveys and applies their feedback to directly improve their product or service.
In this case, the factory is improved by exploring the probability of different outcomes and weighing up which is best. This is performed in a continuous loop: the suggestions emerging from the DT’s insights are realised in real time on the factory floor and then fed back into the DT for as long as the DT is active.
In short, a factory DT can help establish a deeper understanding of manufacturing processes by establishing closed feedback loops. Let’s see what this looks like specifically on assembly lines.
Digital twins on assembly lines
One of the most valuable ways of implementing digitals twins in manufacturing is on assembly lines, as these require high efficiency and connections between numerous processes.
A communication in Automation presents different approaches for how DTs can improve efficiency on assembly lines. Automation was recently accepted into Web of Science’s Emerging Sources Citation Index (ESCI).
Firstly, similar to the virtual testing described above, the authors discuss virtual commissioning. This involves testing single components and functions of a system using virtual models and methods. This helps detect errors in the engineering, design, or programming of manufacturing systems at early stages. This is ideal for reducing the time and costs of the physical commissioning process.
Second, DTs can help in assembly line balancing. Assembly lines require highly complex automation methods that link together different processes smoothly. DTs can be used to test and optimise the distribution of tasks between different assembly stations. This can be linked to different aims, such as maximising assembly line output or testing out a different order of tasks during assembly.
One example of how DTs can improve assembly line balancing is for bin-picking systems. These involve the process of picking parts that are stored arbitrarily in boxes or bulks and placing them in a defined way. This can be practised and tested in simulations before implementation to ensure it does not disturb production.
Using digital twins with robotics
The third example the authors provide is for digital twins supporting human‒robot interaction.
They describe the aim of combining the capabilities of humans with the advantages of automation and robotics. Humans can react flexibly and intelligently to unexpected tasks and therefore have fast and high adaptability, whilst robots have advantages in speed, repeatability, endurance, and strength.
Implementing human‒robot interaction can help automate repetitive tasks whilst retaining humans’ ability to adapt. However, this can pose safety risks. This could mean robot machines may need separating from human workers using screens or even sensors that shut them down when people are in proximity. This may take up larger portions of space and hinder the potential for human‒robot interaction to function seamlessly.
Therefore, industrial robots can be integrated into DTs to identify potentially risky areas and see where they would benefit the assembly line most. Using a DT in this way increases the transferability of research into practice by showing it practically.
Digital twins in manufacturing
To summarise, integrating digital twins in manufacturing can help improve efficiency by freeing the testing phase from the constraints of time and space, increase efficiency by using predictive data to establish closed feedback loops, and can support the implementation of technology like robotics.
DT technology therefore has a lot of potential in manufacturing. However, in other fields, implementation is more complicated. In healthcare, DTs engender a range of ethical concerns relating to privacy and morality. If you want to learn more about how DTs can and are being implemented in healthcare and the ethical concerns surrounding it, read our article Applying Digital Twin in Healthcare.
If you are interested in submitting research on the topic of digital twins, we have plenty of journals that may interest you, such as Machines and Automation.