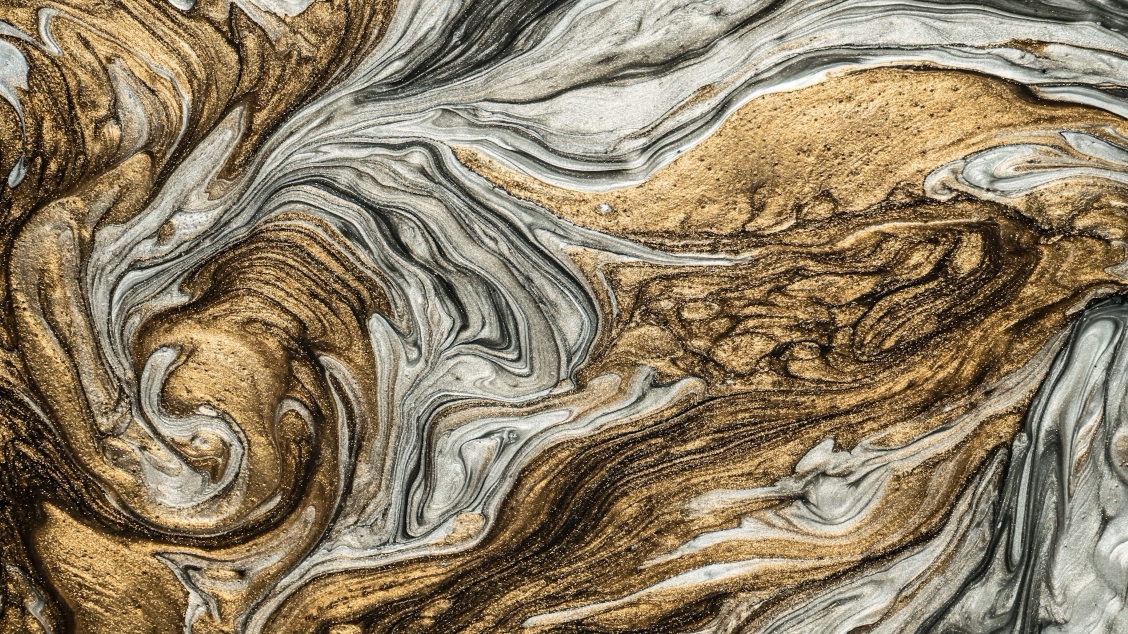
Bubble Printing of Liquid Metal to Improve Flexible Electronics
Wiring technology plays an integral role in our daily life. It has important uses like connecting electrical devices to power sources or carrying signals between devices. Wiring technology typically uses solid aluminium or copper wires and rigid circuit boards. These traditional setups pose challenges for the growing demand for wearable technologies, which could benefit from more flexible wiring technologies.
A new Editor’s Choice article by researchers from Yokohama National University, Japan, published in the Open Access journal Nanomaterials explores bubble printing of liquid metals as an alternative to traditional wiring.
Conventional wiring technologies rely on rigid conductive materials, which are unsuitable for flexible electronics that need to bend and stretch – Professor Shoji Maruo, an author of the study.
Bubble printing method
Bubble printing is a method used to pattern and create high-precision wiring, usually for flexible electronics. The technology uses a laser beam in a liquid to generate a steady flow of bubbles around which the metal particles aggregate. Previously, studies focused on using solid metal particles to generate conductive patterns.
However, the new study published by Mukai et al. reports that bubble printing using liquid metal colloids (dispersed particles) can produce conductive patterns.
Liquid metals provide both flexibility and high conductivity, yet they present issues in wiring size, patterning freedom, and electrical resistance of its oxide layer. – Assistant Professor Masaru Mukai, first author of the study.
Testing bubble printing with liquid metal
The researchers were able to successfully pattern liquid metal colloids onto a glass substrate. To do this, they set up an optical laser system which consists of a femtosecond laser and a Galvano scanner, which reflects the laser in 2D patterns. Here, the laser would then pass through a splitting cube onto a glass substrate to generate conductive lines on the non-conductive surface.
In the study, eutectic gallium-indium (EGaIn) colloids were used to generate the conductive lines. Unlike other studies, the researchers were able to improve the conductivity of the material by immersing it in a silver nitrate solution. This meant that the surface oxide particles were replaced with conductive silver particles. This type of process is referred to as the galvanic replacement of metals.
Furthermore, the researchers saw how the laser beam was able to generate a conductive line using EGaIn colloids, with the EGaIn aggregating around bubbles and along the laser trajectory. The resulting fine line was confirmed as conductive.
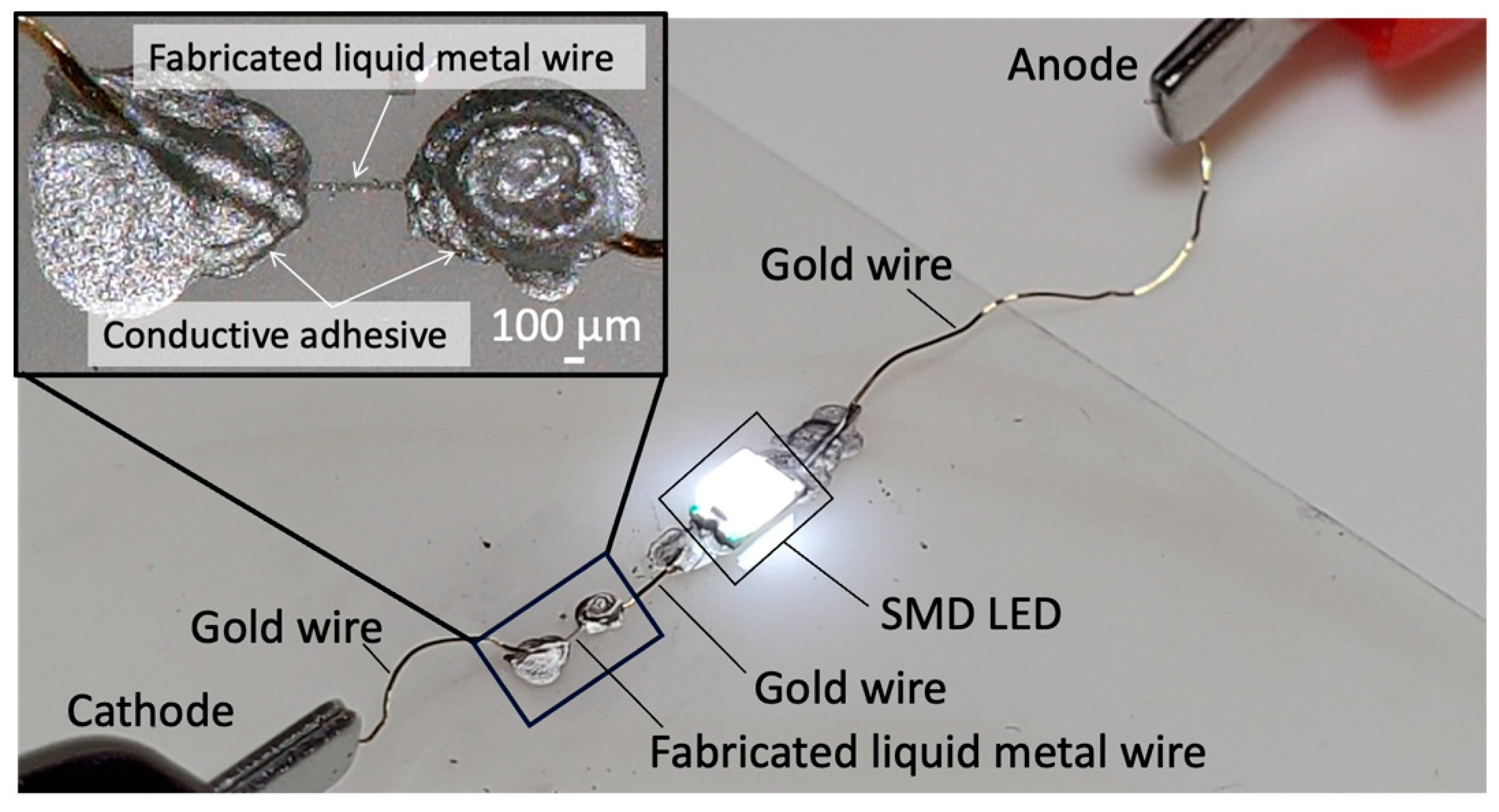
Our liquid metal wiring, with a minimum line width of 3.4 μm, demonstrated a high conductivity of 1.5 × 105 S/m and maintained stable conductivity even when bent, highlighting its potential for flexible electronic applications – Assistant Prof. Mukai
Applications of bubble printing technology
Bubble printing technology could be highly useful in developing wiring for flexible technology, specifically wearable sensor devices, such as smart watches, electronic skin patches, and many other healthcare applications.
Our ultimate goal is to integrate this method with electronic components, such as organic devices, enabling practical, flexible devices for everyday use,” Maruo said. “We see potential applications in areas like wearable sensors, medical devices, and other technologies that require flexible, durable wiring – Assistant Prof. Maruo
Liquid metal wiring provides a promising new approach to powering the future generations of wearable technologies and other electronic devices. To learn more about research like this, access the journal Nanomaterials to explore some of the latest technologies, or access MDPI’s journal list where all articles are free to read immediately.